At ø58 x 58mm long, this massive motor is expressly configured with a ø6 x 42mm
long motor shaft (ø10mm internal) for 600/700-class model helicopters
and thus, isn't supplied with a fixed-wing prop-adapter or mounting
hardware. That said, these accessories are readily available, and this
motor is fantastic for airplane-use as well.
Unlike motors where a button-pusher monitors an automated winding machine loaded with multi-strand wire, this one is hand-wound with a single-strand (8-turns) of ø1.23mm
wire. This requires special tools and a skilled craftsman,
effectively making it a custom motor. Since winding the 12-tooth stator
by hand is finicky and time consuming work, this is a limited production
item so please call for availability.
Packing
the stator poles with thick wire is what gives this motor the ability
to handle a lot of current - e.g. perform a lot of work. After all, the
sole reason for using a single-strand is achieving maximum performance.
Anyway, depending on the
battery pack, this motor is well suited for scale, sport, hot-sport, and
extreme-3D maneuvers.
At 495g and capable of outputting 4250W (about 5.69
hp), what results is sufficient power reserve for pretty much any
maneuver you can imagine. By way of comparison, an OS MAX 1.05HZ-R
engine on 30% nitro makes about 3.75 hp. However, it weighs 596g and costs $530 (plus another $230 for the 185g muffler).
Finally, a suitable ESC (electronic speed control) will typically be of 120-200A capability, and due to the high specific power output, you'd be well advised to lubricate the bearings (a wear item not covered by warranty) each time you go to the flying field (a needle oiler makes this quite easy - these are readily available at hobby shops that cater to RC cars and trucks).
Too Long; Didn't Read (TL;DR)
This
is a seriously good motor because it makes monster power, has huge
bearings, and is hand wound with a single strand of wire. It's called a
Pmax because it's the maximum diameter motor, which you can comfortably
stuff into the
the side frames of a Pantera P6. However, it works pretty darn good with
a lot of 700-800 class helicopters plus fixed wing models (but you have to source your own prop adapter, which
is easy enough).

Background:
Physically
imposing and larger than the usual 4035-type motor, we've found it's
nearly Ideal when matched to the Pantera airframe by dint of it's
versatility. Especially when dynamically loaded with the Quattro rotor
head (4-blades) equipped with two sets of 700s because it has gobs of
torque. Moreover, if you subsequently mount the mechanics within a scale
fuselage, then you have the makings of a superb scale machine (or leave
it pod-n-boom for a hooligan's dream).

- A tight fit, at 58mm this is the maximum diameter motor that fits Pantera side frames

Available
in a range of Kv (450, 520, 630, and 720) this
is our top-of-the-range motor. We hope you delight in using it as much
as we do because within limits, it can almost be thought of as dial-a-motor.
For example, in a helicopter, once you select the basic rotor-head
RPM-range you desire, you can dial the power up or down via the cell
count and thus, totally change its personality. Dealing with just one variable
is nice! Anyway, here are some rule of thumb figures for main rotor
RPMs.
- 8S ~1300 RPM (scale use, 2 or 4-blade head)
- 10S ~1650-1925 RPM (sport, mild-3D)
- 12S ~2100-2250 RPM (extreme-3D)
Here's the math:
First,
let's take a 450Kv motor as an example; Kv is a constant that basically
means the motor output (RPMs) vary with voltage. In this case, 450Kv
means 1volt = 450 RPM (but technically,
Kv (lowercase v) is K=constant multiplied by v=velocity (as opposed to KV which is
Kilo Volts). Anyway, knowing the Kv is handy. In the case of the 450, it means on an
8-cell LiPo pack (nominally 29.6V) this motor
will theoretically turn about 13,320RPM (450x13,320). However, in
the real world it's results in something different.
Fudge factor: or why theory and practice differ
There's
some background math involved (quite a lot) but assessing an 85% fudge
factor will get you close enough for the real world with an
effective load. Note, some call this overall efficiency (the
combination between ESC efficiency, motor efficiency, and prop or rotor blade efficiency). We prefer to
use the term fudge factor because it's derived from our experience.
Anyway, as it turns out, 85% is a pretty valid
rule of thumb when loading the motor near it's max amp rating. Thus, 450Kv x 8cells x 3.7V/cell x 0.85(85% fudge factor)
=11,322RPM . . . and this is surprisingly close in the real world
regardless of whether you're using the rotor blades of a
helicopter, or a propeller, as the load.
Disclaimer:
By
the way, we know to be careful with throwing efficiency numbers around. For example, the motor's efficiency isn't always what we say. If
we're overloading the motor e.g. beyond the proper current
range, then efficiency will be impaired. Similarly, running the motor
with reduced load, impairs efficiency as well. This last seems
utterly counterintuitive because
we expect heat when operating the motor with a load, and conventional
DC motors without a load don't get hot, but a brushless motor without a
load gets hot. What's with that?
Delving
into the subject leads you to learn it has to do with the magnetic field
changing
(inducing current into the iron)/. Thus, under low or no load
conditions you have a multitude of dead shorts hiding inside the center
of your motor! This has to do with the flow of current within the iron
laminations (in the stator core). The current is dissipating as energy (and thus,
producing heat). This is also known as eddy current or iron losses.
But the
point is, theoretical efficiency basically goes out the window in the real world so please just accept
the .85 fudge factor as something that will put you in the ballpark
with real world loaded RPMs. Hence, using a
fudge factor gives good practical results and this is important - especially recalling what a great wag once said on the subject:

Gear Ratios:
In a fixed wing application, e.g. direct drive, there's a 1:1 ratio between motor RPM and load (propeller) - e.g. the RPM of the prop - duh! However, with a helicopter, specifically a Pantera, the gear ratio is 8.7:1. Thus, for an 8S pack
11,322/8.7 = 1300RPM. This is nearly ideal for scale operations where the
goal is to simulate the 600-800RPM for the full scale machine more
closely than you can with a 2000RPM main rotor. By the way, with good throttle management this is good for maybe
8-9 minute flights.
450Kv on 10S
Now
take the same 450KV motor on 10S (37V). It's going to turn the main rotor
at about 1625RPM, which as it happens, is hunky-dory for sport
aerobatics. So just by varying cell count we change the personality - see what we mean by dial a motor? Anyway, as it happens, maneuvers like loops, rolls, and stall
turns, plus flips and tumbles are the sweet spot for 1600-1650RPM range.
So basically, on 10S you get plenty
of poop for sport aerobatics. By the way, 'plenty of poop' is techno-speak
for approximating an OS 55-class nitro engine, e.g. just about the
perfect amount of power for a Pantera P6 model. This is enough to
effortlessly cruise around for up to 7-8 minutes on a
5000mAh pack. Believe it or not, this is plenty of air time for nearly
anybody. So the 450Kv motor on 10S is a very nice combination because you get
sweet performance at an affordable cost. What happens on 12S?
450Kv on 12S
Basically,
operating a Pantera P6 on 12S with a 450kv motor will really perk up
the performance (into the aggressive sport, or mild-3D range). The rotor
speed goes up to about 1925RPM but now the flight time decreases to
maybe 5-1/2 minutes.
Want to know what else the 450Kv motor is
great for? A classic pattern plane with an 11x7 prop (where you're going
to see abut 17,000RPM). You'll have a rocket ship on your hands. One
that will bellow like a bull and roar across the sky (and make every
head turn). Fun? Oh no . . . it's 'great' fun!
520Kv motor
So
what happens if you use the 520KV motor instead? On a 10S pack, with
the 8.7:1 gear ratio of a Pantera (or divide by the gear ratio of whatever helicopter you have in mind), this gives you about 1875RPM. This gives
sparkling aerobatic performance (and flight time goes
up a little bit, to maybe 6-1/2 minutes). Alternatively, stuff a 12S pack in there and
now you're going to see about 2250RPMs, which is what you want for crazy
3D performance range - not just tick-tocks but 'climbing' tick-tocks!
630Kv motor
You may also opt for the 630KV motor on 10S instead of a 12S pack. This will decrease
weight and with around 2275RPM the model will flip and roll so fast it's
a blur (note; 3D stick-bangers absolutely love this combination). Alternatively,
switch to an 8S pack and you're looking at 1825RPM, or sport performance again. Dial-a-motor! Anyway, this is plenty of RPM for sport aerobatics - plus - flight duration goes up to maybe
7-1/2 to 8 minutes. Perhaps this is more your cup of tea!
720Kv motor
What
about the 720Kv motor? Now the theory is 720RPM/volt but otherwise the math is exactly the same. Thus, on an 8S pack it's 720x8x3.7x.85)/8.7 so you'll see 2100RPM, which gives sparkling 3D performance. Depending on the pack capacity and collective management you may see around 6
minutes.
However, if you opt for a 6S pack for this motor, then the rotor head is gonna drop to around
1560RPM. Now we're in the range of sporting maneuvers. E.g. a lot of hovering, cruising around, with the odd loop or roll thrown in. This is absolutely a perfect combination if you like relaxed loafing around for long duration flights (of
maybe 8-9 minutes, maybe more depending on how aggressive you are).
By the way, in
a fixed wing model, the 720Kv is nice on a 6S5000mAH pack because
you'll see 13,500RPM which is the sweet spot for a lot of 13x8-14x6
props.
Summary:
Astonishingly, all this comes out of the same basic motor! The key is hand winding different gauge wire. It's a stunningly simple system for making a fantastic motor!
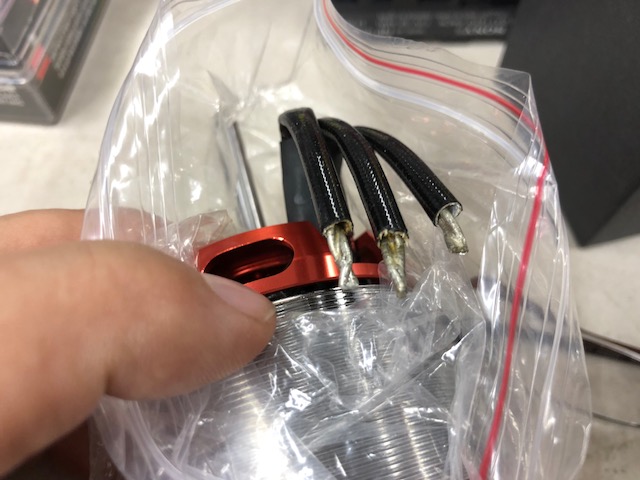
- One single piece of wire loops in and back out in an AabBCcaABbcC pattern

Mechanical details:
The rotor features Neodymium magnets (NdFeB) radially arrayed within the body. And
these strong rare earth magnets are secured within the rotor with high temperature
epoxy. Your goal is to operate it below 260°F. Exceeds the max of 350°F and it's gonna be toast. You've been warned.
Also, the rotor has been
dynamically balanced (to 30K RPM). This, by the way is the purpose of the blue
epoxy (balance weight) in the photo below. Anyway, all this hand-built care is what
you're paying for - the seamless and smooth delivery of pure power.
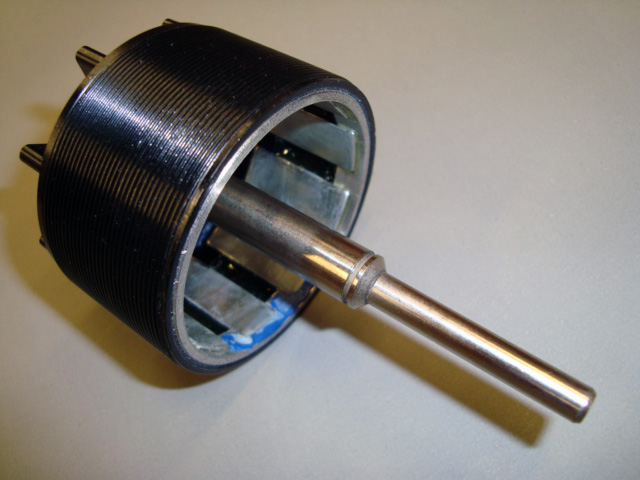
- Massive 10mm shaft - rotor is dynamically balanced
(blue epoxy) to 30K RPM

Anyway, packing
the 12-tooth stator with a single-strand of motor wire for high power handling, combined
with the best magnets, plus the effort of balancing the rotor for high RPMs
(so it won't buzz your electronics to death with vibration), along with 10mm
bearings and what results is a Pmax. You get with power delivery that's smooth as
silk, which is a really, really nice combination from this Delta-wound motor.
Bottom line? This motor is bad ass whether you're using it to power a helicopter or for fixed wing applications.